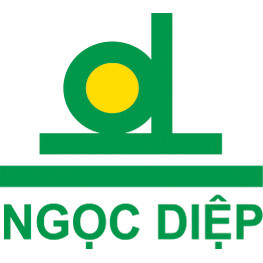
Mô tả công việc
JOB SUMMARY
- Provide leadership and supervision in the project engineering team and facilities maintenance team in support of the engineering department and company goals. Develop personnel, processes and procedures, and provide the necessary technical expertise to complete construction especially in M&E and facility improvement projects; safely, on time, as specified, and under budget.
ESSENTIAL DUTIES & RESPONSIBILITIES
- Set up maintenance program and direct the activities of the maintenance personnel to ensure proper care and maintenance of all equipment.
- Plans, develops, and implements new methods and procedures designed to improve operations, minimize operating costs, and effect greater utilization of labor and materials.
- Complete and maintain reports, such as time and production records, inventories, and test results.
- Recommend or initiate personnel actions, such as employment, performance evaluations, promotions, transfers, discharges, and disciplinary measures.
- Establish or adjust work methods and procedures to meet production schedules, using knowledge of capacities of machines, equipment, and personnel.
- Monitor operations, and inspect, test, and measure completed work, using devices, such as hand tools, gauges, and specifications to verify conformance to standards.
- Patrol work area and examine tools and equipment to detect unsafe conditions or violations of safety rules.
- Direct, coordinate, and assist in performance of workers' activities, such as engine tune-up.
- Recommend measure, such as procedural changes, service manuals revisions, and equipment purchases, to improve work performance and minimize operating costs.
- Confer with personnel, such as management, engineering, quality control, customers, and workers' representatives to coordinate work activities and resolve problems.
- Examine object, system, or facilities, such as ACMV system, or industrial plant, and analyze information, to determine installation, service, or repair needed.
- Request materials and supplies, such as tools, equipment, and replacement parts for work activities.
- Compute and estimates actual costs of factors, such as materials, labor, and outside contractors, and prepares budgets.
- Assigns workers to perform activities, such as service appliances, repair and maintain vehicles, and install machinery and equipment.
- Train workers in methods, procedures, and use of equipment and work aid, such as blueprints, hand tools, and test equipment.
Education
- BS in engineering degree in a related technical field of study or equivalent experience required especially in ACMV and electrical systems. Related technical courses, vendor training, and company specific courses desirable
- Certified Project supervision Class 1 issued by the local government authorities concerned.
Experience
- 4 or more years of maintenance management level experience and ACMV/electrical substation required
- Hands-on mechanical, electrical, and electronic experience required
- Experience utilizing computerized maintenance systems required
Knowledge of:
- Knowledge of MEP design standards and construction especially in the field of ACMV and electrical systems.
- Knowledge of machines and tools, including their designs, uses, repair, and maintenance.
- Knowledge of business and management principles involved in strategic planning, resource allocation, human resources modeling, leadership technique, production methods, and coordination of people and resources.
- Knowledge of principles and procedures for personnel recruitment, selection, training, compensation and
Yêu cầu công việc
Education
- BS in engineering degree in a related technical field of study or equivalent experience required especially in ACMV and electrical systems. Related technical courses, vendor training, and company specific courses desirable
- Certified Project supervision Class 1 issued by the local government authorities concerned.
Experience
- 4 or more years of maintenance management level experience and ACMV/electrical substation required
- Hands-on mechanical, electrical, and electronic experience required
- Experience utilizing computerized maintenance systems required
Knowledge of:
- Knowledge of MEP design standards and construction especially in the field of ACMV and electrical systems.
- Knowledge of machines and tools, including their designs, uses, repair, and maintenance.
- Knowledge of business and management principles involved in strategic planning, resource allocation, human resources modeling, leadership technique, production methods, and coordination of people and resources.
- Knowledge of principles and procedures for personnel recruitment, selection, training, compensation and benefits, labor relations and negotiation, and personnel information systems.
- Knowledge of the structure and content of the English language including the meaning and spelling of words, rules of composition, and grammar.
- Knowledge of the practical application of engineering science and technology. This includes applying principles, techniques, procedures, and equipment to the design and installation of electro-mechanical system and services.
Skills and Abilities
- Ability to work independently, organize and prioritize work.
- Dependable
- Detail and accuracy oriented
- Ability to problem solve
- Team Player
- Confident, firm personality
- Ability to control a high pressure situation
EQUIPMENT USED
- Welding machines
- Powered hand tools
- Electrical testing instruments
- Mechanical testing instruments
MENTAL & PHYSICAL DEMANDS/WORKING CONDITIONS
1. Mental Effort
- The ability to maintain a concentrated effort over extended periods of time.
- Ability to meet deadlines
- Attention to detail
2. Physical Requirements
- Stand frequently
- Walk frequently
- Use hands, wrists, and arms continuously
- Reaching above shoulders occasionally
3. Working Conditions
This position involves working in general manufacturing conditions where there are continuously moving mechanical parts. These conditions also include working in an area where airborne particles and/or finishing fumes are present, along with continuous loud noise from the manufacturing processes involved in creating wooden parts to engineering specifications. None of these conditions are present to the point of being disagreeable.
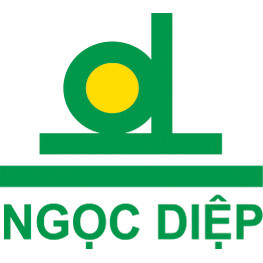
Khởi đầu từ Trung tâm nội thất văn phòng, gia đình, trường học từ năm 1996, Ngọc Diệp lần lượt mở rộng sang các lĩnh vực Bao bì carton (1998), Cửa (2010), Nhôm (2016). Năm 2017, Ngọc Diệp tái cấu trúc theo mô hình Tập đoàn, trong đó Công ty Cổ phần Tập đoàn Ngọc Diệp giữ vai trò là Công ty mẹ cùng các Công ty thành viên.
Tập đoàn Ngọc Diệp bao gồm 4 công ty thành viên: Công ty TNHH Thương mại và Sản xuất Ngọc Diệp; Công ty Cổ phần Ngọc Diệp; Công ty Cổ phần Cửa Ngọc Diệp và Công ty Cổ phần Nhôm Ngọc Diệp.
Ngọc Diệp đang vươn mình phát triển trở thành Tập đoàn hàng đầu về sản xuất, cung ứng các sản phẩm Nội thất, Bao bì, Cửa nhôm - cửa nhựa - vách mặt dựng, Nhôm công nghiệp - Nhôm xây dựng. Các sản phẩm của Tập đoàn Ngọc Diệp có mặt rộng khắp 63 tỉnh thành.
Chính sách bảo hiểm
- Được hưởng chính sách bảo hiểm xã hội, bảo hiểm y tế, bảo hiểm thất nghiệp,….
- Được tham gia bảo hiểm tai nạn cá nhân 24/24
Các hoạt động ngoại khóa
- Du lịch hằng năm
- Teambuilding
- Các hoạt động vui chơi giải trí, thể thao
Lịch sử thành lập
- Được thành lập vào năm 2017
Mission
-
TẦM NHÌN – SỨ MỆNH: Là một trong những tập đoàn đa ngành hàng đầu Việt Nam, Tập đoàn Ngọc Diệp cam kết cung cấp những sản phẩm mang thương hiệu Ngọc Diệp với chất lượng uy tín, mang lại những giá trị gia tăng cao nhất cho cổ đông, đối tác, người lao động và xã hội.
-
GIÁ TRỊ CỐT LÕI :Xây dựng thương hiệu bằng uy tín, chất lượng;Không ngừng đổi mới, sáng tạo;Coi trọng con người, đề cao sức mạnh đoàn kết;Phát triển kinh doanh song hành cùng trách nhiệm xã hội.
Những nghề phổ biến tại Ngọc Diệp Group
Bạn làm việc tại Ngọc Diệp Group? Chia sẻ kinh nghiệm của bạn
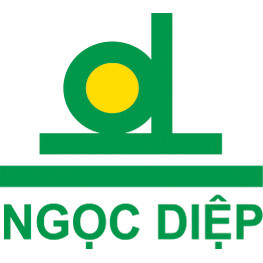