Tìm thấy 9 việc làm đang tuyển dụng
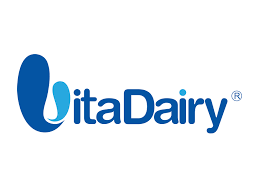
Planning Executive - Australian Company In Binh Duong
Thông tin cơ bản
Mức lương:
Thỏa thuận
Chức vụ:
Nhân viên
Ngày đăng tuyển:
Đang cập nhật
Hạn nộp hồ sơ:
14/10/2024
Hình thức:
Toàn thời gian
Kinh nghiệm:
Không yêu cầu
Số lượng:
1
Giới tính:
Không yêu cầu
Nghề nghiệp
Ngành
Địa điểm làm việc
- Lot A 3.1 Dong An 2 Industrial Zone, Thu Dau Mot, Binh Duong
Tính chất công việc
Full-time
Vị trí/chức vụ
Nhân viên/Chuyên viên
Yêu cầu bằng cấp (tối thiểu)
Thạc sỹ
Yêu cầu kinh nghiệm
Không yêu cầu
Ngày đăng tuyển
12/09/2024
Số lượng tuyển
Không giới hạn
Yêu cầu ngôn ngữ
Không
Yêu cầu độ tuổi
Không
Yêu cầu giới tính
N/A
Kĩ năng
Thu Mua , Lập Kế Hoạch
Mô tả công việc
Planning
• Consolidation of sales forecasts from international and local sales networks into monthly demand charts to drive material planning functions and monitor/modify this demand according to all influencing factors.
• Preparation of work centre production schedules to ensure timely completion to finished goods based on forecast and actual requirements by optimising daily production lists. Schedules must reflect practical, optimised, and efficient plans that take account of market requirements, immediate requirements, material availability, plant capacity, direct labour availability, safety stock levels and finished goods holdings.
• Distribution of product to international branches in line with forecast and stock holding requirements. Ensure the production of goods are available to meet sales orders for local and export orders, specifically:
o Basing on Sales Forecast and BOM to build MRP database to calculate raw material demands for productions.
o Creating all reports in MPS to control materials for production by linking with Materials Master Data, to monitor forecast, PO, planning, production, delivery, production versus planning, delivery versus PO and sales forecast.
o Meeting weekly with Production to review and adjust/ issue updated production planning.
o Manage and provide counsel to the employees of departments under direct control.
o Maintain a high level of personal contact and interaction with personnel in all departments to ensure efficiency of communication.
o Provide advice to other departments where requested in relation to forecast volumes, potential issues, stocking levels, etc.
o Manage and negotiate with the logistics department related to transportation for local, interstate and wharfage requirements where required with the aim of minimising costs and providing efficient service to the business.
o Manage and report on inventory levels within the organisation to improve operating cost. Work with and advise the managers of the various warehouses in controlling and maintaining appropriate inventory levels.
o Co-ordinate and support the stocktaking and cycle counting programs of the organisation with the aim of minimising inventory variance and maintaining inventory accuracy.
o Coordinating with the ERP party to build and improve ERP and inventory and data base systems.
• Using problem solving techniques develop and address issues affecting the planning, distribution and inventory processes utilising the operational team.
• Manage and reduce working capital by working with all production departments to optimise inventory levels for both raw materials and finished goods. Reduce and improve to eliminate over-building of finished goods.
• Maintain a high level of housekeeping within the designated areas of responsibility.
• Ensure regular/daily meetings are held to ensure a high level of communication within all departments, as well as internal and external customers.
• Production breakdowns or line stoppages may occur from time to time. Liase with production to ensure a catch-back within 3 days.
• Container loading scale to optimise and minimise transportation costs
• Plan in advance to avoid disruptions related to public holidays.
Import Export
• Co-ordinate and ensure Logistics team have planned and ordered deliveries, containers, trucks on time.
• In the event production cannot meet the planned delivery schedule, ensure that Purchase Orders can be repurposed with alternate stock/ mixed load - avoid losing revenue within the set period (month), or giving up the container.
• Co-ordinate with Purchasing Officers to follow closely all incoming materials related to Purchase Orders to ensure on-time production.
• Co-ordinate with Purchasing Officers to follow closely all incoming goods related to outbound shipments to ensure on-time production.
• Co-ordinate all exporting and local shipments or deliveries to ensure on time delivery for customers.
• Co-ordinate with Warehouse Officers and Logistic Officers to ensure outbound deliveries are exact match to order, on-time, and safely despatched.
• All delivery backlogs must be reported weekly to senior management and the Financial controller and General Director. All backlogs that could not be met according to the frozen plan should have that quantity where possible substituted as an alternate product mix. All backlogs to be completed within the next month without impacting the next month's original forecast (no reductions in supply quantities and must include the additional backlog).
Other responsibilities
• Support other Departments to solve the problems.
• Other tasks assigned by your superiors.
Key Performance Indicators:
• Champion and hold at no later than, arrangement and holding Monthly meetings with external customers and internal/external sales teams to catch up on selling trends that could impact planning, purchasing, and all aspects of production execution.
• Champion daily and hold at no later than, weekly meetings with the internal customers: Manufacturing, Engineering, Labour, Quality; to consider manpower availability, setting daily build rate schedules, readjustment and notification of Daily Production Plans and coordinate with logistics in arranging shipping schedules.
• Reduced Changeovers (by SKU, by model group with the plan to reduce forced changes that could affect delivery schedules)
• Development and maintenance of Daily Production Schedules based on Standard Hours (and Target Hours) defined per SKU
• Co-ordinate with the production scheduler/planner on Daily Production plans issued into production work centers:
o Press Shop,
o Heater (all production lines)
Welding Lines,
Enameling and Furnace,
Storage Centre after furnace,
Heater Assembling,
o Kits, Spare Parts and Sub-Assemblies feeding sales or internal production centers
o Collector,
Schlatter Plates,
Absorber Plates
Folded Tray Assembling
Envelope Assembling
o Heat Pump Modules
o Heat Pump Heater Assembling
o Other centres as the business expands.
• Responsible and Accountable for Backlog Reporting.
Issue weekly report of materials, including reasons why reporting with corrective actions, that:
o impact a change to the production schedule.
o materials that have not arrived on time according to the production schedule.
o delays in production affecting planned deliveries.
o Quantity of goods not delivered within the month - include updated date of planned delivery.
• Inventory reduction and minimum warehouse storage of Finished Goods
• Sustain a Weekly Stable Container plan established to reduce burden and risk of container disruption
• Increase Stock Turns via improved planning
• Reduce Stock Out - incoming purchased components and outgoing short supply to customer, re-adjust production build of assigned SKUs and ensure on time delivery and revenue generated within assigned month
• OTIF: On Time In Full
• DSA: Delivery Schedule Accuracy
• MSA: Manufacturing Schedule Accuracy
• Daily Production SKU Accuracy
• Other KPIs and maintenance of DASHBOARDS assigned by superiors.
• Consolidation of sales forecasts from international and local sales networks into monthly demand charts to drive material planning functions and monitor/modify this demand according to all influencing factors.
• Preparation of work centre production schedules to ensure timely completion to finished goods based on forecast and actual requirements by optimising daily production lists. Schedules must reflect practical, optimised, and efficient plans that take account of market requirements, immediate requirements, material availability, plant capacity, direct labour availability, safety stock levels and finished goods holdings.
• Distribution of product to international branches in line with forecast and stock holding requirements. Ensure the production of goods are available to meet sales orders for local and export orders, specifically:
o Basing on Sales Forecast and BOM to build MRP database to calculate raw material demands for productions.
o Creating all reports in MPS to control materials for production by linking with Materials Master Data, to monitor forecast, PO, planning, production, delivery, production versus planning, delivery versus PO and sales forecast.
o Meeting weekly with Production to review and adjust/ issue updated production planning.
o Manage and provide counsel to the employees of departments under direct control.
o Maintain a high level of personal contact and interaction with personnel in all departments to ensure efficiency of communication.
o Provide advice to other departments where requested in relation to forecast volumes, potential issues, stocking levels, etc.
o Manage and negotiate with the logistics department related to transportation for local, interstate and wharfage requirements where required with the aim of minimising costs and providing efficient service to the business.
o Manage and report on inventory levels within the organisation to improve operating cost. Work with and advise the managers of the various warehouses in controlling and maintaining appropriate inventory levels.
o Co-ordinate and support the stocktaking and cycle counting programs of the organisation with the aim of minimising inventory variance and maintaining inventory accuracy.
o Coordinating with the ERP party to build and improve ERP and inventory and data base systems.
• Using problem solving techniques develop and address issues affecting the planning, distribution and inventory processes utilising the operational team.
• Manage and reduce working capital by working with all production departments to optimise inventory levels for both raw materials and finished goods. Reduce and improve to eliminate over-building of finished goods.
• Maintain a high level of housekeeping within the designated areas of responsibility.
• Ensure regular/daily meetings are held to ensure a high level of communication within all departments, as well as internal and external customers.
• Production breakdowns or line stoppages may occur from time to time. Liase with production to ensure a catch-back within 3 days.
• Container loading scale to optimise and minimise transportation costs
• Plan in advance to avoid disruptions related to public holidays.
Import Export
• Co-ordinate and ensure Logistics team have planned and ordered deliveries, containers, trucks on time.
• In the event production cannot meet the planned delivery schedule, ensure that Purchase Orders can be repurposed with alternate stock/ mixed load - avoid losing revenue within the set period (month), or giving up the container.
• Co-ordinate with Purchasing Officers to follow closely all incoming materials related to Purchase Orders to ensure on-time production.
• Co-ordinate with Purchasing Officers to follow closely all incoming goods related to outbound shipments to ensure on-time production.
• Co-ordinate all exporting and local shipments or deliveries to ensure on time delivery for customers.
• Co-ordinate with Warehouse Officers and Logistic Officers to ensure outbound deliveries are exact match to order, on-time, and safely despatched.
• All delivery backlogs must be reported weekly to senior management and the Financial controller and General Director. All backlogs that could not be met according to the frozen plan should have that quantity where possible substituted as an alternate product mix. All backlogs to be completed within the next month without impacting the next month's original forecast (no reductions in supply quantities and must include the additional backlog).
Other responsibilities
• Support other Departments to solve the problems.
• Other tasks assigned by your superiors.
Key Performance Indicators:
• Champion and hold at no later than, arrangement and holding Monthly meetings with external customers and internal/external sales teams to catch up on selling trends that could impact planning, purchasing, and all aspects of production execution.
• Champion daily and hold at no later than, weekly meetings with the internal customers: Manufacturing, Engineering, Labour, Quality; to consider manpower availability, setting daily build rate schedules, readjustment and notification of Daily Production Plans and coordinate with logistics in arranging shipping schedules.
• Reduced Changeovers (by SKU, by model group with the plan to reduce forced changes that could affect delivery schedules)
• Development and maintenance of Daily Production Schedules based on Standard Hours (and Target Hours) defined per SKU
• Co-ordinate with the production scheduler/planner on Daily Production plans issued into production work centers:
o Press Shop,
o Heater (all production lines)
Welding Lines,
Enameling and Furnace,
Storage Centre after furnace,
Heater Assembling,
o Kits, Spare Parts and Sub-Assemblies feeding sales or internal production centers
o Collector,
Schlatter Plates,
Absorber Plates
Folded Tray Assembling
Envelope Assembling
o Heat Pump Modules
o Heat Pump Heater Assembling
o Other centres as the business expands.
• Responsible and Accountable for Backlog Reporting.
Issue weekly report of materials, including reasons why reporting with corrective actions, that:
o impact a change to the production schedule.
o materials that have not arrived on time according to the production schedule.
o delays in production affecting planned deliveries.
o Quantity of goods not delivered within the month - include updated date of planned delivery.
• Inventory reduction and minimum warehouse storage of Finished Goods
• Sustain a Weekly Stable Container plan established to reduce burden and risk of container disruption
• Increase Stock Turns via improved planning
• Reduce Stock Out - incoming purchased components and outgoing short supply to customer, re-adjust production build of assigned SKUs and ensure on time delivery and revenue generated within assigned month
• OTIF: On Time In Full
• DSA: Delivery Schedule Accuracy
• MSA: Manufacturing Schedule Accuracy
• Daily Production SKU Accuracy
• Other KPIs and maintenance of DASHBOARDS assigned by superiors.
Yêu cầu công việc
• A certificate in Materials Management, Purchasing, Supply chain, Planning is preferred
• Minimum 7 years previous management experience in manufacturing and or distribution with significant exposure to demand planning, production planning and distribution in a "make-to-order" or "make-to-stock" environment.
• Previous experience or extensive knowledge of inventory control practices, policies and procedures.
• Microsoft computer software usage, especially on Excel..
• Good in using ERP system, preferably SAP.
• Excellent organization, and planning skills and analytical skills..
• Good written and verbal communication in English and analytical skills.
• Ability to perform under pressure.
• Minimum 7 years previous management experience in manufacturing and or distribution with significant exposure to demand planning, production planning and distribution in a "make-to-order" or "make-to-stock" environment.
• Previous experience or extensive knowledge of inventory control practices, policies and procedures.
• Microsoft computer software usage, especially on Excel..
• Good in using ERP system, preferably SAP.
• Excellent organization, and planning skills and analytical skills..
• Good written and verbal communication in English and analytical skills.
• Ability to perform under pressure.
Quyền lợi được hưởng
Thưởng
Annual leave, Insurances and Policies following Labor Law ( Gross salary for insurances )
Chăm sóc sức khoẻ
Competitive salary, shuttle bus ( Binh Dương ), Laptop, Meal , Milk ( 48 cartons), Uniform..
Máy tính xách tay
24/24 Insurance, 02 rotating Saturday off, training policy, cheering party, 13th salary...
Annual leave, Insurances and Policies following Labor Law ( Gross salary for insurances )
Chăm sóc sức khoẻ
Competitive salary, shuttle bus ( Binh Dương ), Laptop, Meal , Milk ( 48 cartons), Uniform..
Máy tính xách tay
24/24 Insurance, 02 rotating Saturday off, training policy, cheering party, 13th salary...
Khu vực
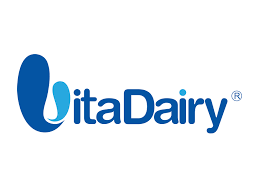
VITADAIRY
Xem trang công ty
Quy mô:
200 - 500 nhân viên
Địa điểm:
Được thành lập bởi các Y Bác sĩ, Dược sĩ và các chuyên gia Dinh dưỡng đầu ngành, VitaDairy tự hào là doanh nghiệp luôn tiên phong trên hành trình mang đến những giá trị dinh dưỡng khoa học góp phần nâng cao sức khỏe và cải thiện chất lượng cuộc sống cho hàng triệu người tiêu dung Việt Nam
Từ khi thành lập, VitaDairy đã xác định và lựa chọn hướng đi khác biệt chính là mang đến nền tảng sức khỏe vững chắc cho người Việt, đặc biệt là thế hệ trẻ. Chính vì vậy, làm thế nào để các sản phẩm dinh dưỡng giúp tăng cường miễn dịch để có Hệ miễn dịch khỏe, điều kiện tiên quyết cho sự phát triển toàn diện cho thế hệ tương lai của đất nước đã được VitaDairy lựa chọn và tập trung nghiên cứu trong nhiều năm qua.
Chính sách bảo hiểm
- Các chính sách về bảo hiểm bắt buộc, trợ cấp, khám sức khỏe,...
Các hoạt động ngoại khóa
- Hoạt động giải trí:
- dã ngoại và du lịch cùng Công ty
- thể thao & các hoạt động ngoài trời;
- Được tham gia các hoạt động gắn kết của công ty.
Lịch sử thành lập
- Được thành lập năm 2018 bởi các Y Bác sĩ, Dược sĩ và các chuyên gia Dinh dưỡng đầu ngành, VitaDairy tự hào là doanh nghiệp luôn tiên phong trên hành trình mang đến những giá trị dinh dưỡng khoa học góp phần nâng cao sức khỏe và cải thiện chất lượng cuộc sống cho hàng triệu người tiêu dung Việt Nam
Mission
- Sự nghĩ khác làm mới của VitaDairy không chỉ dừng lại ở việc luôn đổi mới sản phẩm, làm mới những phân khúc hiện có của thị trường để đưa đến những giải pháp hoàn hảo cho người tiêu dùng. Cập nhật xu thế cuộc sống số luôn thay đổi hàng ngày cùng khát vọng giao tiếp trực tiếp với khách hàng, ứng Dụng QR Code - Đổi muỗng nhận quà của VitaDairy đã chạm tới trái tim của khách hàng khi là ứng dụng mang đến nhiều thông tin và lợi ích nhanh nhất và kịp thời , đạt gần 1 triệu lượt download (tải về) chỉ sau thời gian ngắn ra mắt và được ghi nhận tại lễ vinh danh Top Công nghiệp 4.0 Việt Nam - I4.0 Awards năm 2022 hạng mục Top doanh nghiệp có sản phẩm số thông minh và giải pháp công nghệ công nghiệp 4.0.
Review VITADAIRY
3.0
1 review
07/07/2022
★
★
★
★
★
IT Officer
tại Hồ Chí Minh
Đa số nhân viên công ty toàn u30 trở lên chiếm nhiều nên môi trường không hợp mấy bạn trẻ như chúng mình đâu các bạn. (rv)
Những nghề phổ biến tại VITADAIRY
Bạn làm việc tại VITADAIRY? Chia sẻ kinh nghiệm của bạn
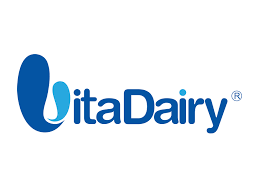
VITADAIRY
Click để đánh giá